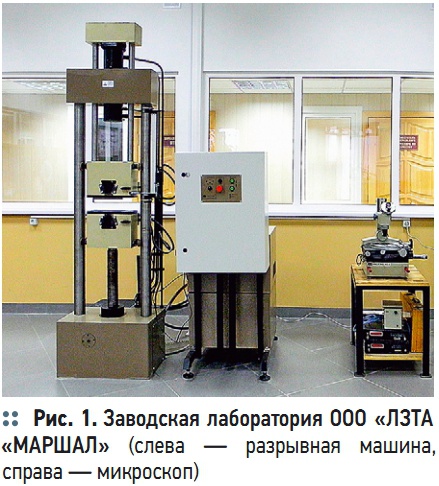
Рис. 1. Заводская лаборатория ООО «ЛЗТА «МАРШАЛ»
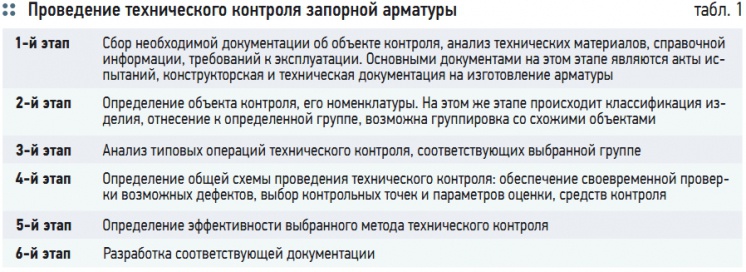
Табл. 1. Проведение технического контроля запорной арматуры
Классификация технического контроля включает в себя входной, операционный и приемочный виды контроля; визуальный и измерительный; а также другие виды и способы. Очередность проведения данного комплекса мероприятий можно представить следующим образом (табл. 1). При визуальном контроле проводится проверка соответствия арматуры спецификации и другой необходимой технической документации; наличия маркировки; отсутствия на корпусе повреждений, трещин или коррозии; наличия защитного покрытия на поверхности изделия; состояния сварных швов.
Измерительный контроль включает оценку присоединительных размеров арматуры; параллельность фланцев между собой; массу арматуры, а также толщину стенок изделия; и отклонения измеряемых размеров должны быть в рамках требований, указанных в технической документации. Конечно, для проведения измерительного контроля необходимы соответствующие инструменты. Например, контроль толщины стенок корпусных деталей рекомендуется определять ультразвуковым методом.
А масса арматуры определяется при проведении периодических испытаний путем взвешивания на весах по ГОСТ 29329, как среднее значение трех результатов взвешиваний. В заводских лабораториях также проводятся испытания материалов на разрыв, на ударную вязкость, испытания на стойкость к коррозии, металлографические исследования, измерения толщин покрытий арматуры. Одним из этапов контроля является определение ее герметичности.
Существуют различные способы подобного контроля — жидкостный и газовый, в зависимости от рабочей среды, которая будет использоваться при испытаниях. Рассмотрим, например, жидкостный метод контроля. Поверхность арматуры должна быть очищена от загрязнений или ржавчины, затем просушена, недопустимо появление влаги на корпусе арматуры.
При проведении контроля первоначально удаляют воздух из внутренних частей арматуры, которые далее заполняются рабочей испытательной средой. Давление в исследуемых изделиях должно повышаться/ понижаться постепенно. После окончания испытания из арматуры удаляют испытательную среду, а затем промывают и просушивают. Данный метод контроля применяется с целью определения места расположения повреждения или дефекта арматуры.
Водой создается определенное давление, прописанное в конструкторской документации, и на поврежденных участках арматуры возможно возникновение капель или влажных пятен. Другой метод — соединение арматуры с жидкостной полостью гидропневмоаккумулятора. После заполнения водой в газовой полости повышают давление. По понижению давления в газовой или жидкостной полостях можно судить об обнаружении повреждений, дефектов или разгерметизации частей арматуры.
Как видно из вышесказанного, существует большое количество методов, способов и видов технического контроля для обеспечения безаварийной работы трубопроводов. Совершенствуются и сама запорная арматура и методы ее технического контроля, что приводит к снижению опасных ситуаций на производстве и повышению качества надежности эксплуатации трубопроводных систем.