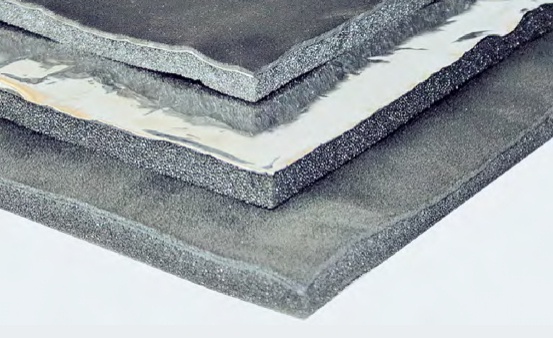
Во второй половине семидесятых годов прошлого века получила признание технология эмалирования труб. На начальном этапе производство принципиально выглядело так: труба очищалась от ржавчины, обжигалась и нагревалась с помощью индукционных редукторов. В раскаленном состоянии (красного цвета) она подавалась под покраску — в виде порошка на нее напылялась стеклоэмаль. Покрытие получалось тонким (несколько микрон), но эффективным, поскольку эмаль по отношению к металлу обладает хорошими адгезионными свойствами. В дальнейшем эмаль на трубу стали наносить с помощью специальной ванны.
Эволюция изолирующих покрытий
Несмотря на то, что технология эмалирования труб в конце двадцатого века была передовой, проблема сохранности теплопроводов так и оставалась нерешенной. Само стеклоэмалевое покрытие при погрузочно-разгрузочных и монтажных работах получало сколы из-за своей хрупкости, и в этом месте образовывалась точечная коррозия. Несоизмеримо с действительностью возрастали требования к культуре производства — с эмалированной трубой необходимо было обращаться крайне бережно.
Применялась старая минераловатная теплоизоляция, сварные стыки так и оставались неэмалированными, хотя для этих целей была разработана специальная передвижная установка, способная в полевых условиях нанести эмаль на стыки. Установка представляла собой «КамАЗ» с двухосным прицепом, и большие габариты лишали ее возможности применения в стесненных условиях городской застройки мегаполиса. От установки пришлось отказаться.
Для изоляции стыков использовались несколько различных видов мастик, но и это не принесло удовлетворительного результата: принципиально разные по составу материалы (стеклоэмаль и мастика) не могли обеспечить необходимую адгезию. Дальнейшее использование эмалированных труб в строительстве теплотрасс было приостановлено. Следующим этапом эволюции противокоррозионной защиты стала технология покрытия стальных труб алюминием: методом газоплазменного напыления алюминий в виде порошка наносился на наружную поверхность трубы слоем около 300 мк.
Это т.н. «технология алюминирования»: трубу второй степени очистки, практически белую, очищенную дробометом (с помощью дроби), подавали в камеру с установленным плазмотроном, где и происходило напыление цветного металла. Затем для уплотнения пористой структуры напыленного алюминия трубу покрывали кремнийорганическим лаком. Алюминиевое покрытие по стойкости не уступало эмалевому, превосходило его по эластичности: при ударе и механическом воздействии на трубу на алюминиевом покрытии не образовывалось сколов.
Но эффективная изоляция стыков по-прежнему оставалась нерешенной проблемой: их места не алюминировались, а лишь покрывались кремнийорганическим лаком. Теплоизоляция так же оставляла желать лучшего — минеральная вата или плита армировались сеткой-рабицей и покрывались асбестоцементной мастикой. После этих этапов в производство конструктива тепловых сетей постепенно стал проникать пенополиуретан (ППУ), до этого времени использовавшийся в основном в оборонной промышленности.
С применением полимера появилась возможность сочетать в одной технологической цепочке защиту трубы от коррозии и ее теплоизоляцию. Выглядело это следующим образом. Труба помещалась в специальную камеру и вращалась на роликах, над ней по рельсам двигалась каретка, из которой на трубу подавались два компонента — полиол и изоцианат.
Приближенный к поверхности трубы наиболее пористый слой пенополиуретана служил для теплоизоляции, удаленный (наружный) — более плотный, напоминающий скорлупу, с большим количеством закрытых пор (его получали изменением соотношения реагентов) — герметизировал конструкцию. Для изоляции фасонных изделий и мест стыков использовались изготовленные из ППУ, сообразно размерам изолируемых элементов, «скорлупы». Их приклеивали на мастику.
Но и эта технология годилась только для канальной прокладки, поскольку не обеспечивала необходимой защиты от коррозии. Поворотным стал 1997 г. — в Россию пришла актуальная для нашей страны технология производства предварительно изолированных труб для тепловых сетей — «труба в трубе». От предыдущей технологии настоящую кардинально отличает заливочное оборудование и принцип заливки: полимер поступает не просто на наружную поверхность изолируемой трубы, а в полость между стальной внутренней трубой и пластиковой внешней оболочкой под давлением 200 атм.
Процесс смешивания компонентов (полиола и изоцианата) происходит не на трубе, а в заливочной головке установки. ППУ заполняет весь объем между трубой и оболочкой практически без образования раковин. В течение последующих трех лет производство носило статус экспериментального. С применением труб в ППУ изоляции были реконструированы три участка теплотрасс, которые находились под пристальным наблюдением инженеров. Технология «труба в трубе» отлично зарекомендовала себя.
Производственный контроль качества труб в ППУ-изоляции
С точки зрения соблюдения параметров качества конечного изделия наиболее трудным является производство фасонных изделий. Нарезка трубы на сегменты должна осуществляться только на механическом отрезном станке, поскольку газовая резка в местах реза меняет структуру металла — он становится хрупким. В принципе в таком случае предполагается его зачистка на глубину не менее 5 мм, но проконтролировать этот факт зачастую невозможно.
К тому же в процессе сваривания деталей также невозможно установить — присутствовала необходимая зачистка или нет. Механическая резка трубы уменьшает влияние человеческого фактора на качество изделия. Крайне важно, как внутри теплоизоляции изделия будет располагаться контрольный провод — это напрямую скажется на дальнейшей эксплуатации теплопровода. По всему периметру фасонного изделия, как и прямой трубы, устанавливаются центрирующие опоры, на которых крепится контрольный провод.
Но, учитывая, что ППУ с большой скоростью заполняет объем между стальной трубой и полимерной оболочкой и этот процесс закрыт от вмешательства человека, становятся возможными дефекты расположения контрольного провода. В частности, на первый взгляд незначительное увеличение длины контрольного провода вследствие его перекручивания относительно оси трубы (в конкретной плоскости), когда провод превышает длину трубы или элемента, при дальнейшей эксплуатации трубопровода сказывается на увеличении погрешности в определении потенциального места аварии.
Исходя из приобретенного опыта нормальной считается погрешность в пределах 1 % от расстояния тестируемого трубопровода (3–4 м на участке протяженностью 300–400 м). В случае применения некондиционных элементов — с удлиненными (перекрученными) контрольными проводами — погрешность достигает 3–4 %, что не только многократно увеличивает стоимость только землеройных работ, не считая стоимости увеличенного количества машино-часов, оплаты труда, работ по благоустройству территории, но и зачастую в стесненных городских условиях не позволяет расположить даже строительную технику.
Часто требуется получать не одно и не два дополнительных разрешения на ведение работ, а гораздо больше, ввиду пролегания теплотрассы по территориям нескольких собственников. Поэтому, чем точнее (относительно запроектированного) в изделии располагается контрольный провод, точнее производится монтаж и заделка стыков (в частности, соединение контрольных проводов), тем более объективной будет картина работы теплопровода, получаемая мониторингом системы ОДК.
В этом случае контроль качества труб и фасонных изделий приходится вести с помощью метода неразрушающего контроля — рентгеноскопическим прибором, встроенным в производственную линию. Благодаря этим мерам удается снизить коэффициент повреждаемости трубопроводов (учитывая только зависящие от производителя параметры качества) с 0,7–0,8 на начальной стадии применения новой технологии до 0,07 на сегодняшний день. Все специалисты строительных субподрядных организаций — производителей работ — проходят обязательное обучение принципам правильного монтажа трубопроводов из предизолированных труб. Но все это лишь одна сторона вопроса.
Практика эксплуатации
системы ОДК Далеко не везде в нашей стране научились эксплуатировать систему оперативного дистанционного контроля состояния теплопроводов. Эксплуатирующие организации по разным причинам не спешат осваивать новую технологию. Наилучшее положение с эксплуатацией системы ОДК в Москве. Замерами — мониторингом системы — занимается независимая от эксплуатационных компаний организация. Но финансирование сферы коммунального хозяйства даже в Москве недостаточно для того, чтобы догнать, тем более — опередить старение теплопроводов.
В российских регионах положение еще более удручающее. Главная задача руководителя конкретной эксплуатирующей службы — бесперебойное обеспечение потребителей теплом. Поэтому на практике из его поля зрения преимущественно выпадает мониторинг показаний системы ОДК нового, только что проложенного, теплопровода — тепло-то он в любом случае доносит до потребителей, а факт намокания теплоизоляции или обрыв сигнального провода отходят на дальний план.
Ведь система призвана диагностировать предаварийные ситуации на ранней стадии, что автоматически означает наличие в резерве достаточного количества времени до проявления самого худшего — сквозной коррозии трубопровода. Аварийных же теплопроводов, не снабженных системой ОДК, абсолютное большинство. Именно установка бесконечного количества заплаток, постоянные сливы и перезапуск отопительных систем до сих пор остаются главным в деятельности конкретных эксплуатирующих служб.
Чтобы предупредить такую сложную и неприятную ситуацию, в Москве мониторингом показаний системы ОДК занимаются специализированные компании. Свои отчеты специалисты этих компаний периодично представляют всем заинтересованным сторонам коммунального сектора экономики и городского хозяйства — от управленцев эксплуатирующих и подрядных организаций до руководства муниципального округа, района. Замолчать в этом случае результаты контроля показаний системы или оставить их без внимания просто невозможно за счет достигнутой прозрачности в предоставлении данных эксплуатации системы ОДК.