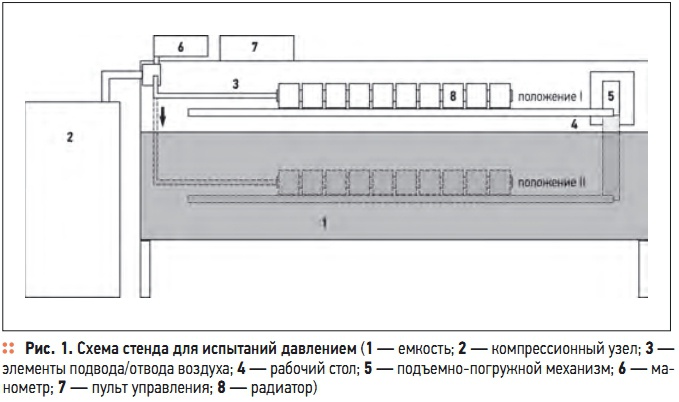
Рис. 1. Схема стенда для испытаний давлением
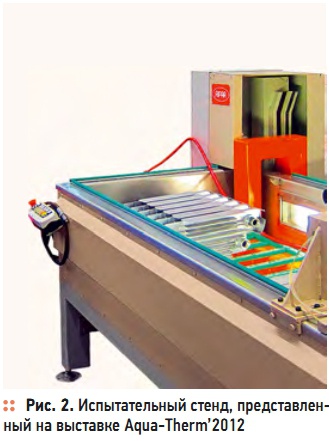
Рис. 2. Испытательный стенд, представленный на выставке Aqua-Therm’2012
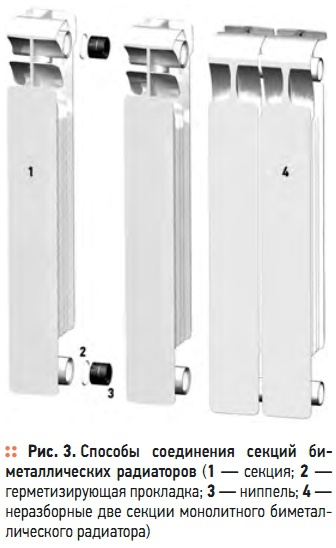
Рис. 3. Способы соединения секций биметаллических радиаторов
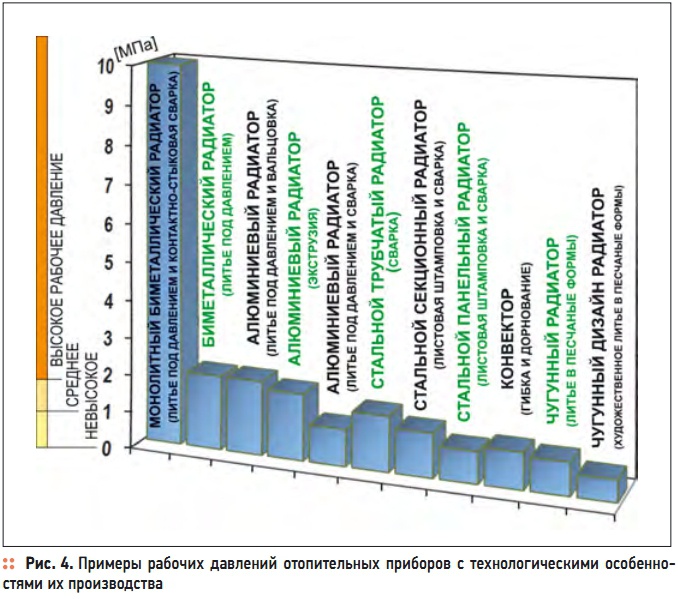
Рис. 4. Примеры рабочих давлений отопительных приборов с технологическими особенностями их производства
Сегодня производство радиаторов систем водяного отопления по разработкам, конструктивным особенностям изделий, применяемым технологиям и материалам не уступает высокотехнологичным областям, таким как машиностроение, а порой и превосходит их. Ведь, несмотря на кажущуюся простоту формы и принципа работы, радиаторы должны отвечать самым строгим требованиям.
И касаются они не только эффективной отдачи тепла от теплоносителя в помещение, но и обеспечения продолжительного срока службы, на который прямо или косвенно влияют разные факторы — резкие перепады температуры, избыточное давление, агрессивная среда теплоносителя, локальные силовые нагрузки из-за нарушения правил монтажа и др. Кроме того, учет практики применения отопительной техники ставит перед разработчиками новые задачи.
В частности, все более актуальны вопросы обеспечения комфортного микроклимата в каждом помещении путем устранения излишнего поступления тепла, эффективного перераспределения и использования всей тепловой энергии, экономии энергоресурсов, внедрения систем автоматического управления. Их решение возможно благодаря снабжению радиаторов индивидуальными средствами регулировки теплоотдачи — термоклапанами, термостатическими регуляторами, интеллектуальными датчиками и т.д.
Для применения таких устройств подходит не любой радиатор. Обусловлено это тем, что прибор должен быстро изменить параметры теплоотдачи в зависимости от установленных на регулирующих элементах значений. Снабжать этими элементами целесообразно только радиаторы, обладающие малой инерционностью. Следуя требованиям времени, производитель отопительных приборов учитывает все эти частные и общие пожелания в своей продукции.
При этом использует как накопленный производственный опыт, так и уникальные новейшие разработки, последние достижения, в т.ч. из других областей — робототехники, химической промышленности, приборостроения и др. Заданный темп совершенствования технических характеристик радиаторов означает для производителя не только внесение конструктивных изменений при сохранении сложившихся норм внешнего вида, не только использование прогрессивных технологий, систем автоматизации и привлечение высокоточного оборудования, но и соответствие новым требованиям к контролю качества на всех стадиях изготовления — от выбора исходного материала до отгрузки готовой продукции заказчику.
Контроль установлен для химического состава сырья, плавки, механических свойств, резьбовых и сварных соединений, толщины и качества покраски, шероховатости поверхностей, параметров упаковки, условий складирования и многого другого. Средства контроля также должны проходить постоянную проверку. Поэтому производство современного отопительного прибора невозможно без проведения комплекса контроля качества.
Производство радиаторов регулирует ГОСТ 31311–2005 «Приборы отопительные» [1]. В частности, согласно п. 5.2 отопительные приборы должны быть прочными и герметичными, и выдерживать пробное давление воды или воздуха, превышающее не менее чем в полтора раза максимальное рабочее давление, но не менее 0,6 МПа. Для контроля соответствия этому требованию производитель использует специальные испытательные стенды.
Максимальное рабочее давление должно быть указано в паспорте на радиатор [1, 2]. Рассмотрим стенд для испытаний давлением при контроле воздухом с погружением прибора в емкость. Стенд схематично изображен на рис. 1 и состоит из емкости 1, компрессионного узла 2, элементов подвода воздуха 3, рабочего стола 4, подъемно-погружного механизма 5, манометра 6, пульта управления 7, испытуемого радиатора 8. Порядок действий при работе на этом стенде следующий.
Радиатор 8 размещают на рабочем столе 4 (положение I). Герметизируют внутреннюю полость радиатора 8. Затем подключают радиатор 8 с помощью элементов подвода/отвода 3 к компрессионному узлу 2. После этого через пульт управления 7 подают команду подъемно-погружному механизму 5, погружают радиатор 8 в жидкость (положение II) и включают компрессионный узел 2 на подачу воздуха. При достижении на манометре 6 давления, равного испытательному, срабатывает специальная автоматика поддерживающая это давление в заданном промежутке времени.
Далее клапан в компрессионном узле 2 снижает давление в радиаторе до атмосферного. Затем через пульт управления 7 подают команду на подъемно-погружной механизм 5. Радиатор 8 поднимается над водой (положение I). После отключения элементов подвода/отвода 3 радиатор 8 перемещают с рабочего стола 4 и отправляют на следующую операцию. Во время испытания контролируют наличие утечки воздуха. Если по достижении уровня испытательного давления утечка воздуха отсутствует, то радиатор признается прошедшим контроль.
В случае, если выявлена утечка воздуха, радиатор отправляется на переработку. Контроль и управление может выполнять (в зависимости от оснащенности испытательного стенда) оператор или специальная автоматическая система. Следует обратить внимание на то, что испытания пробным давлением каждый отопительный прибор проходит дважды. Первичный контроль — после сборки до операции окраски, второй — перед упаковкой и отправкой потребителю.
Таким образом, производственный контроль радиатора на стенде гарантирует не только надежность сборки, но и прочность, герметичность прибора при эксплуатации с давлением до значений рабочего. Иногда фактом поиздельного испытания радиаторов пробным давлением пренебрегают. Так, при попытке самостоятельной или в сторонней организации перекомпоновки секционных радиаторов нужно учитывать, что в этом случае производитель не может гарантировать безотказную работоспособность прибора.
Несомненно, внепроизводственное испытание давлением жидкости позволит проконтролировать герметичность радиатора, но ответственность за его исправность во время работы должен возложить на себя исполнитель. Связано это не столько с примитивностью его оборудования по сравнению с промышленным, сколько с тем, что могут оказаться неучтенными некоторые параметры. Например, конструктивные: в конструкции ряда секционных радиаторов существуют особенности сочетания элементов соединения и герметизации.
Известно, что межсекционное соединение состоит из непосредственно секций, ниппеля и герметизирующей прокладки (рис. 3). Особенности конструкции предполагают, что эти элементы при сборке в месте стыка секций образуют полость, где располагается герметизирующая прокладка. Профиль прокладки с учетом ее упругих свойств и профиль полости на производстве подобраны очень точно, чтобы компенсировать действующее давление и обеспечить долгий срок службы соединения.
Возможные ошибки сборщика при самостоятельной перекомпоновке связаны с выбором герметизирующей прокладки: использовать старую или установить новую. В первом случае прокладка может не обеспечить герметизацию, так как произошла ее малая необратимая деформация; во втором случае легко ошибиться при подборе геометрических и механических свойств прокладки. Следует учитывать и усилие соединения секций. При производстве величина этого усилия задана и строго соблюдается.
Рабочее давление — характеристика для сравнения радиаторов, но для выбранной группы отопительных приборов (чугунные, алюминиевые, стальные, биметаллические секционные, стальные панельные радиаторы, конвекторы и др. [3, 4]) его величина существенно не различается. Это связано с тем, что для каждой группы отопительных приборов свойственны особенности, обусловливающие уровень рабочего давления.
Выделим основные: форма — габариты, размер и расположение каналов, поверхностей теплопереноса; конструктивный материал — алюминиевый сплав, сталь, чугун; технология производства — литье в песчаные формы, литье под высоким давлением, экструзия, листовая штамповка, гибка, дорнование труб, сварка. На характеристиках могут сказаться: внедренные ноу-хау; технический уровень оборудования, применяемого при изготовлении; политика качества и ответственности на производстве.
Условное сравнение рабочего давления отопительных приборов приведено в виде диаграммы на рис. 4; отметим, что значения могут меняться в зависимости от производителя и модели по указанным выше причинам. Из представленных выделим три группы отопительных приборов: с высоким, средним и невысоким рабочим давлением. Минимальное давление характерно для чугунных и панельных радиаторов, максимальное — для монолитных биметаллических радиаторов.
Взаимосвязь рабочего давления и типа отопительного прибора рассмотрим на примере конструктивных и технологических особенностей монолитного биметаллического радиатора [5], позволяющего заявлять в сравнении с аналогичным секционным прибором максимальное рабочее давление в 10 раз больше. Монолитный биметаллический радиатор состоит из стального закладного элемента, который под высоким давлением заливают алюминиевым сплавом.
В результате получается одна секция, обладающая всеми преимуществами группы биметаллических (сталь и алюминий) радиаторов. Принципиальным отличием монолитного радиатора является способ сборки секций. Если обычно секции соединяют с помощью ниппелей и герметизирующих прокладок, то в данном случае используют контактно-стыковую сварку. Нужно отметить, что получаемый соединительный шов имеет существенные отличия от «произвольного» сварного шва.
Это обусловлено не только особенностями оборудования, оснастки для контактно-стыковой сварки, но и использованием специальных технологических режимов. Например, при периоде сварки около секунды параметры подвода тока задаются строго функционально в зависимости от времени. При таком соединении секций, то есть без применения резьбового соединения с ниппелем и без использования материалов с низким показателем стойкости к нагрузкам — герметизирующих межсекционных прокладок, отопительный прибор может выдерживать существенно более высокое давление, сохраняя герметичность.
Учитывая, что в системе отопления часто используют различные устройства и компоненты с рабочим давлением до 10 атм, монолитный биметаллический радиатор имеет 10-кратный запас для безотказной работы. В заключение следует отметить, что на фоне общего стремительного развития отопительной техники на практике выбор радиатора все более усложняется из-за множества функциональных и конструктивных различий каждого.
При этом испытания пробным давлением, проводимые заводом-изготовителем, и величина рабочего давления — среди главных факторов, определяющих безотказную работу вашего радиатора в соответствии с заданными параметрами системы отопления.